Load Cell Manufacturer Force Measurement Tests
Force measurement testing is one of the most critical processes that Load Cell manufacturers use to ensure their products meet key mechanical and structural requirements. Force measurement tests are used to measure a material’s response to an applied force. Prior to production, a Load Cell manufacturer starts with an approved design, followed by an established manufacturing process, and a proven test plan to ensure success.
Load Cell Stress-Strain Design Considerations
Understanding the Stress-Strain curve is key to Load Cell design, material selection, and testing. Key considerations include Young’s modulus, Yield Strength (YS), and Ultimate Tensile Strength (UTS). Load Cell “Factor of Safety” may be based on either its YS, UTS, or both. The selection of the most suitable Load Cell material depends on the Stress-Strain curve, as well as several other factors.
- Elastic Region. Load Cells are designed to operate normally and repeatably within the Elastic Region. In this region, materials exhibit a nearly linear, repeatable, spring-like behavior as quantified by its Young’s modulus (also called the modulus of elasticity or its proportionality constant). Hooke’s Law is used as a linear approximation to describe this spring-like behavior. Stresses applied to material within this region will cause a small amount of reversible deformation. Once the stress is removed, the material will return to its original shape and size.
- Yield strength (YS). Yield strength is also called the proportionality limit. Applied stress above this limit will start to permanently deform the Load Cell material. This overload condition will result in Load Cell measurements offset from its original pre-yielded condition. This is most apparent when the applied load returns to a zero-load condition and the load cell response is non-zero. Typically, Load Cells are designed with a published “safety overload” value over the specified operating range to allow for unforeseen overload conditions.
- Ultimate Tensile Strength (UTS). Ultimate strength (or UTS) is the maximum amount of stress that may be applied to a material before fracture. At this point, many materials will experience necking, where cross-sectional area is reduced locally, and failure can occur. Load Cells are typically manufactured from higher strength UTS materials for greater load carrying capacity. Load Cells are designed for specific factors of safety on material UTS. For example, a Load Cell with a UTS factor of safety of 3:1, will start to fail and eventually fracture if the applied loading force is 3 times or higher than the operating range.
- Both YS and UTS are important not only for the overall macro scale of the Load Cell, but also on all localized areas of the load cell material that physically interface with fixtures or assemblies. Designs must also ensure that bending stresses, shear stresses, and any other stress concentrations are avoided, or permanent deformation or failure could occur.
- Load Cell Materials. Load cells are typically constructed of materials, such as 17-4 stainless steel, alloy steel, and other high-strength materials primarily due to their mechanical properties. Other factors to consider include corrosion resistance, cost and availability, machinability, and cyclic fatigue life expectancy. Fatigue occurs when the stress upon a material is repeatedly loaded and unloaded. Fatigue failure can occur when materials are subjected to excessive cyclic loading at stresses below their YS. Load Cell designs need to include fatigue life expectancy considerations during Load Cell material selection and design.
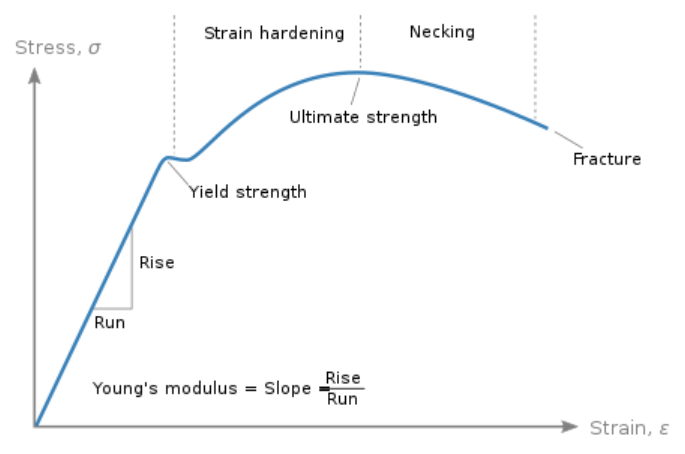
Stress-Strain Curve – Wikipedia
Load Cell Force Measurement Tests Categories
Load Cell testing along the Stress-Strain curve can be broken into 2 distinct test categories, which are non-destructive (NDT) and destructive tests. Load Cell manufacturers must establish and maintain cost effective and timely strategies to meet customer requirements in both categories. This includes both in-sourced and outsourced test resources.
- NDT testing. NDT force tests are performed on all Load Cells and are usually in-sourced. NDT force measurement tests include Calibration, Proof Load, and Hardness. Both Calibration and Proof Load tests must be performed on every Load Cell. Hardness test is a special NDT case where a small permanent indentation is applied to a localized area where performance will not be affected. Hardness test may be in-sourced.
- Destructive testing. Destructive force measurement tests are less frequently required and are typically outsourced to certified test laboratories that can perform the specific tests. These tests involve special procedures, equipment, and certifications, as well as additional cost, time, and material.
Calibration and Proof Load NDT
Calibration and Proof Load tests are the force measurement processes that certify Load Cell conformance to required standards. They are performed during Load Cell production, including the final certified force calibration. Re-calibration of Load Cells is recommended to be performed on an annual basis, per NIST. Re-calibration ensures the Load Cell is operating within standards and provides an opportunity to adjust the output, if necessary. Re-calibration may be done either at the original factory or in-place using reproduceable conditions.
The Calibration Laboratory must include proper environmental conditions, procedures, certified equipment, fixturing, and qualified personnel. To ensure both greater efficiency and tighter quality control, typically in-source qualified personnel are used. Load Cell customers should ensure that the manufacturer’s Calibration Laboratory is able to meet or exceed their requirements.
Calibration Test Equipment
In the Calibration Laboratory, special test machines apply stable, controlled forces to Load Cells. Stress is applied along a single axis in either tension or compression. While stress is being applied, strain is measured using sophisticated electronic test equipment, which is connected to sensor strain gauge bridge circuity.
Examples of Load Cell force measurement types include Tension, Compression, Shear, Bending Beam, and Torque. For these various measurement types, specific fixturing is used to adapt the test machine to the Load Cell. For optimal reproducibility, fixturing must be designed and installed to match the target application as closely as possible.
Additionally, test machines can measure displacement while stress is applied using highly accurate LVDT transducers. Displacement may be monitored to ensure the Load Cell under test is neither elongated nor compressed beyond acceptable limits.
Calibration Tests
During Calibration, multiple force loading values are applied throughout the measurement range of the Load Cell. Loading values increase from zero to full-scale, stopping at each loading value for a strain measurement. In some cases, additional “unloading” measurements are recorded in reverse order decreasing from full-scale to zero. The cycle is then repeated multiple times. The complete table of Load Cell measurements is then collected and analyzed. The analysis typically includes repeatability, non-linearity, and hysteresis.
- Repeatability. Repeatability is the amount of measurement variability while under the same controlled conditions. Measurements are taken by qualified personnel, using the same connections and instruments, and within a relatively short period.
- Non-linearity. Although Hooke’s Law is a linear approximation of Load Cell response, measurement data must be analyzed to ensure that non-linearity does not exceed allowable limits. To improve upon small amounts of non-linearity, correction algorithms may be used.
- Hysteresis. Hysteresis is defined as the dependence of the state of a system on its history. Load Cell hysteresis is analyzed in cases where both loading and unloading measurements are recorded.
Destructive Load Cell Material Tests
In many cases, a customer may require additional Load Cell material testing across the entire Stress-Strain curve up to the point of fracture. Tests are performed on sample material coupons prior to Load Cell manufacturing. These tests can verify Young’s modulus, YS, UTS, and Poisson’s ratio, under a variety of temperature conditions. Testing may also include Fatigue cycle testing, Creep test, Stress Rupture test, Tensile Strength test, and Impact (Charpy, Drop).
Customers requiring additional material testing must ensure that their manufacturer can handle these special requirements. Some manufacturers may only provide off-the-shelf standard Load Cells often sourced from overseas. These low-cost manufacturer options may be suitable for some applications. However, unique, and specific application requirements are becoming increasingly necessary across many industries, where automation and expensive installations must operate reliably. Equipment downtime is not an option. Several industries have led the way, including Aerospace, Mining, Oil & Gas, and Marine.
Force Measurement Solutions
As products become more complex and technologically advanced, the test and measurement industry must provide solutions to monitor a wide variety of factors. This is especially true in force measurement tests of sensors that are meant to be highly reliable, accurate and durable even in extreme environments where failure is not an option.
Strainsert has been involved in force measurement for more than 60 years and follows rigorous standards for testing and calibration of their Load Cells. Strainsert is a leading innovator in the Load Cell industry and holds many U.S. Patents. In addition to our standard Load Cell product line, we are a front-runner in custom Load Cell designs. Custom designs are driven by customer and application requirements. Our custom design experience provides optimal, trusted, and reliable force measurement solutions. To learn more, please contact us online or by calling 610-825-3310 to discuss with our engineering and design teams.